Мы предоставляем индивидуальные решения всем нашим клиентам и предлагаем полные технические консультации, которыми может воспользоваться ваша компания.
Конструкция и материалы экструзионного шнека играют решающую роль в выполнении процесса экструзии.
конструкция и материалы винта могут различаться в зависимости от конкретного применения и свойства экструдируемого материала.
Процесс производства экструзионных шнеков обычно включает в себя этапы проектирования и проектирования, выбора материала, механической обработки, обработки поверхности, контроля и испытаний, а также окончательной упаковки и отправки.
Важно выбрать правильную конструкцию и размер шнека, а также соответствующий шаг и материалы, чтобы обеспечить наилучшую производительность в процессе экструзии.
I. Введение
А. Определение экструзионного шнека
B. Назначение экструзионного шнека
C. Обзор различных типов экструзионных шнеков
II. Дизайн и материалы
A. Одношнековая и двухшнековая экструзия
B. Размер и шаг винта
C. Глубина винта
D. Материалы, используемые в производственном процессе
А. Производство пластмасс
Б. Пищевая промышленность
C. Другие отрасли, в которых используются экструзионные шнеки
А. Проектирование и проектирование
Б. Выбор материала
С. Обработка
Д. Обработка поверхности
Е. Проверка и тестирование
Определение экструзионного шнека
Ан Экструзионный шнек — это устройство, которое используется для перемещения и придания формы материалу, обычно пластику или пищевому продукту, посредством процесса, называемого экструзией. . Шнек обычно изготавливается из металла и помещается внутри цилиндра, также известного как экструдер. Шнек приводится в движение двигателем и вращается, проталкивая материал вперед через цилиндр. Форма шнека может варьироваться в зависимости от типа процесса экструзии и экструдируемого материала. Шнек может иметь один или несколько витков, и его конструкция может влиять на скорость потока, давление и температуру материала, когда он проталкивается через цилиндр.
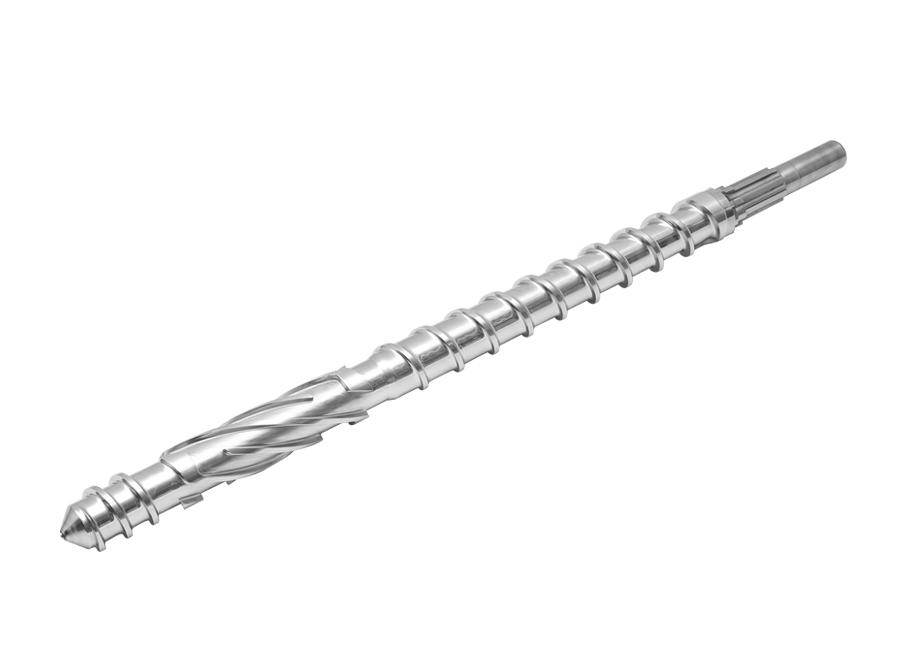
Назначение экструзионного шнека
Целью экструзионного шнека является перемещение и придание формы материалу, который выдавливается через цилиндр экструдера. Шнек предназначен для приложения силы к материалу, проталкивая его вперед и через матрицу на конце цилиндра. Конструкция шнека также может использоваться для контроля давления, температуры и скорости потока материала при его экструзии. Кроме того, шнек можно использовать для смешивания, гомогенизации или нагрева материала во время его экструзии. Экструзионный шнек является важным компонентом процесса экструзии, который используется в широком спектре промышленных применений, таких как производство пластиковых изделий, пищевых продуктов и фармацевтических продуктов.
Обзор различных типов экструзионных шнеков
Существует несколько различных типов экструзионных шнеков, каждый из которых имеет свою уникальную конструкцию и предназначение. Некоторые из наиболее распространенных типов экструзионных шнеков включают в себя:
Одношнековая экструзия : Как следует из названия, этот тип экструзионного шнека имеет одинарный виток или спираль и обычно используется для простых процессов экструзии, когда материал проталкивается через матрицу для достижения определенной формы.
Двухшнековая экструзия : Этот тип экструзионного шнека имеет два параллельных шнека, которые вращаются в противоположных направлениях. Он используется для более сложных процессов экструзии, когда материал необходимо смешивать, нагревать или гомогенизировать во время экструзии.
Шурупы с барьерными пролетами : этот тип шнека предназначен для создания барьера между подаваемым материалом и дозируемым материалом, что позволяет лучше контролировать процесс экструзии.
Шнеки со смесительными элементами : этот тип шнека имеет элементы, которые помогают перемешивать материал при его экструзии, что особенно полезно для материалов, которые имеют тенденцию к расслаиванию или оседанию в процессе экструзии.
Шурупы со штыревыми элементами : этот тип шнека имеет штифтовые элементы, которые увеличивают удельную поверхность материала и способствуют лучшей теплопередаче, что особенно полезно для материалов, которые трудно нагревать.
Винты с рифлеными скребками : этот тип шнека имеет канавки на скребке, которые увеличивают удельную поверхность материала и способствуют лучшей теплопередаче, что особенно полезно для материалов, которые трудно нагревать.
Важно отметить, что тип используемого экструзионного шнека зависит от конкретного применения и свойств экструдируемого материала.
Одношнековая и двухшнековая экструзия
Одношнековая экструзия и двухшнековая экструзия — это два разных типа процессов экструзии, которые обычно используются в различных отраслях промышленности.
При одношнековой экструзии используется один шнек, который вращается внутри цилиндра, проталкивая материал через матрицу для достижения желаемой формы. Этот тип экструзии прост и понятен и обычно используется для материалов, которые легко обрабатывать и не требуют значительных модификаций в процессе экструзии. Одношнековая экструзия обычно используется для производства таких изделий, как трубы, листы и простые профили.
С другой стороны, при двухшнековой экструзии используются два параллельных шнека, которые вращаются в противоположных направлениях. Этот тип экструзии более сложен и позволяет лучше контролировать процесс экструзии. Двойные шнеки можно использовать для смешивания, нагрева или гомогенизации материала во время его экструзии. Этот тип экструзии обычно используется для материалов, которые трудно обрабатывать или которые требуют модификации в процессе экструзии. Двухшнековая экструзия используется для производства таких продуктов, как гранулы, волокна и сложные профили.
Важно отметить, что каждый тип процесса экструзии имеет свои преимущества и недостатки, и выбор того, какой из них использовать, зависит от конкретного применения и свойств экструдируемого материала.
Размер и шаг винта
Размеры и шаг экструзионного шнека являются важными факторами, влияющими на производительность процесса экструзии.
Размеры винта включают диаметр и длину винта. Диаметр шнека обычно выбирается в зависимости от размера цилиндра и экструдируемого материала. Длина шнека определяется количеством материала, который необходимо экструдировать, и желаемой производительностью.
Шаг винта относится к расстоянию между витками или спиралями винта. Шаг может быть постоянным или переменным и влияет на скорость потока материала при его экструзии. Винт с большим шагом будет иметь более высокую скорость потока, а винт с меньшим шагом — меньшую скорость потока. Шаг также влияет на давление, которое винт оказывает на материал: больший шаг приводит к более высокому давлению.
Сочетание размера и шага шнека, а также его конструкции играет решающую роль в производительности, давлении и температуре экструдируемого материала. Важно выбрать правильную конструкцию и размер шнека, а также соответствующий шаг, чтобы обеспечить максимальную производительность процесса экструзии.
Глубина винта
Глубина винта относится к расстоянию между кончиком винта и корнем витков винта. Этот размер также известен как «глубина винтового канала» или «глубина корня винта». Это важный фактор, влияющий на производительность процесса экструзии.
Более глубокий канал шнека позволяет удерживать больший объем материала внутри шнека, что может увеличить производительность экструдера. Однако более глубокий шнековый канал также может увеличить давление внутри цилиндра, что может привести к более высокому энергопотреблению и более высоким температурам экструдера.
С другой стороны, более мелкий шнековый канал может снизить давление внутри цилиндра и снизить потребление энергии, но также может снизить производительность экструдера.
Глубина винта также влияет на теплообмен между винтом и материалом. Более глубокий канал шнека может уменьшить теплопередачу между шнеком и материалом, что может привести к повышению температуры экструдера. С другой стороны, более мелкий шнековый канал может увеличить теплопередачу между шнеком и материалом, что может снизить температуру экструдера.
Таким образом, глубина шнека — это баланс между производительностью и энергопотреблением, баланс должен быть достигнут с учетом свойств материала и желаемого конечного продукта.
Материалы, используемые в процессе производства
Материалы, используемые в процессе производства экструзионных шнеков, могут различаться в зависимости от конкретного применения и свойств экструдируемого материала. Наиболее распространенные материалы, используемые для изготовления экструзионных шнеков, включают:
Сталь : Сталь — прочный и долговечный материал, который обычно используется для изготовления экструзионных шнеков. Он выдерживает высокие температуры и давление, устойчив к износу.
Нержавеющая сталь: Нержавеющая сталь — это устойчивый к коррозии материал, который обычно используется для изготовления экструзионных шнеков в пищевой промышленности.
Закаленная сталь: Закаленная сталь — это тип стали, подвергнутой термической обработке для повышения ее прочности и износостойкости. Он обычно используется для изготовления экструзионных шнеков для абразивных или быстроизнашивающихся применений.
Инструментальная сталь: Инструментальная сталь – это разновидность стали, известная своей высокой износостойкостью и прочностью. Его обычно используют для изготовления экструзионных шнеков для быстроизнашивающихся или абразивных применений.
Сплавы на основе никеля: Сплавы на основе никеля, такие как Инконель и Хастеллой, известны своей устойчивостью к высоким температурам и коррозии. Они обычно используются для изготовления экструзионных шнеков для высокотемпературных или агрессивных применений.
Карбид вольфрама: Карбид вольфрама — очень твердый и износостойкий материал, который обычно используется для изготовления экструзионных шнеков для абразивных или быстроизнашивающихся применений.
Приложения
Производство пластмасс : Экструзионные шнеки используются при производстве широкого спектра пластиковых изделий, таких как трубы, листы и профили. Процесс экструзии используется для плавления пластиковых гранул или гранул и придания им желаемой формы.
Пищевая промышленность: Экструзионные шнеки используются в пищевой промышленности для смешивания, нагревания и придания формы пищевым продуктам. Их обычно используют для производства макарон, сухих завтраков и закусок.
Фармацевтика: Экструзионные шнеки используются для производства таблеток и капсул в фармацевтической промышленности. Процесс экструзии используется для смешивания, нагревания и формования активных ингредиентов и вспомогательных веществ в гранулят, который затем прессуется в таблетки или заполняется капсулами.
Химикаты и удобрения : Экструзионные шнеки используются для производства широкого спектра химической продукции и удобрений. Процесс экструзии используется для смешивания, нагревания и придания сырьем формы желаемого продукта.
Текстильные волокна: Экструзионные шнеки используются для производства широкого спектра текстильных волокон. Процесс экструзии используется для плавления полимера и формирования волокна, которое затем охлаждается и вытягивается.
Древесно-пластиковые композиты : Экструзионные шнеки используются для производства древесно-пластиковых композитов. Процесс экструзии используется для смешивания, нагревания и придания формы древесным волокнам и пластику в композитный материал.
Переработка : Экструзионные шнеки используются для переработки пластиковых отходов путем их плавления, смешивания и формирования нового продукта.
Процесс производства экструзионных шнеков
Проектирование и проектирование: Первым шагом в производственном процессе является создание конструкции экструзионного шнека. При проектировании будут учитываться конкретное применение, свойства экструдируемого материала и желаемый конечный продукт. Инженеры будут использовать специализированное программное обеспечение для создания 3D-модели винта, которая будет использоваться для управления производственным процессом.
Выбор материала: Следующий шаг – выбор подходящего материала для винта. Выбор будет зависеть от конкретного применения и свойств экструдируемого материала. При выборе материала также будут учитываться особые требования к конечному продукту, такие как контакт с пищевыми продуктами, устойчивость к коррозии, устойчивость к высоким температурам и другие.
Обработка: После того, как материал выбран, винт подвергается механической обработке до нужных размеров и формы. Обычно это предполагает использование станков с ЧПУ для вырезания и придания формы винту из цельного куска металла.
Обработка поверхности: После обработки винта его можно подвергнуть процессу обработки поверхности. Это может включать термообработку, азотирование, закалку или другие процессы, которые используются для улучшения износостойкости, коррозионной стойкости и общих характеристик винта.
Проверка и тестирование: Перед отправкой винта покупателю он проверяется и тестируется, чтобы убедиться, что он соответствует спецификациям клиента и не имеет дефектов. Это может включать в себя визуальный осмотр, измерение размеров и функциональное испытание.
Окончательная упаковка и отправка: После проверки и испытания винта его упаковывают и отправляют покупателю. В комплект поставки входит чертеж винта и сертификат соответствия.
Бочкообразные экструзионные шнеки производятся в соответствии с вашим конкретным применением, независимо от производителя OEM. Мы также предлагаем бесплатный расчет экструзионного шнека для наших клиентов.
Бочкообразные экструзионные шнеки производятся в соответствии с вашим конкретным применением, независимо от производителя OEM. Мы также предлагаем бесплатный расчет экструзионного шнека для наших клиентов.